Sustainability at S&C
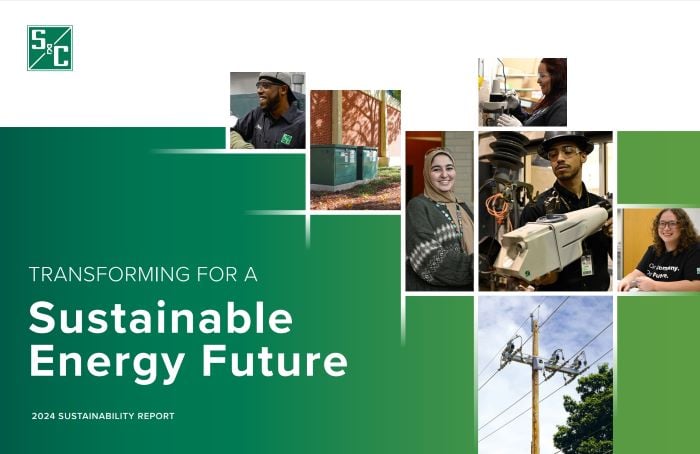
Our Approach
As a privately owned company, S&C has built a strong culture around its values and guiding principles of Personal Integrity, Respect for People, Commitment to Excellence, and Responsible Stewardship. These values reflect our ambition to secure a more sustainable energy future as we uphold the responsibility to address how our business impacts our team members, our communities, and our customers.
Rooted in strong ethics and integrity, S&C demonstrates its commitment to sustainability in its annual Sustainability Report.
Read Latest ReportFor S&C, sustainability means building on our over 100-year-long culture and history of innovation to generate intentional, measurable, and positive impacts for customers, team members, the environment, and the communities we serve. As extreme weather becomes more frequent and our dependence on electricity grows, our sustainability strategy drives us to transform power into purpose. Our innovative technology advances a more intelligent, resilient, and reliable electrical grid and enables a more sustainable, clean energy future.
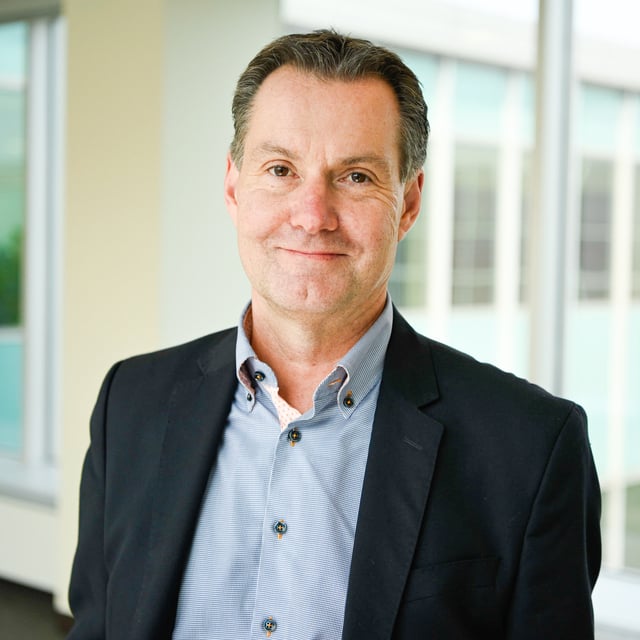
Strategic Sustainability Priorities
Our sustainability priorities are directly aligned with S&C’s corporate strategy, underscoring how sustainability is integrated into the expectations we have of ourselves and of our vision for the future. These priorities include sustaining a people-first culture, our relentless drive for customer-centered innovation, and our goal to achieve the highest standards of operational excellence.
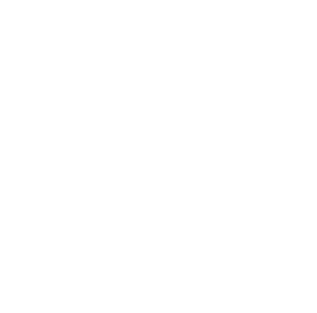
People-First Culture
Fostering an inclusive, people-first culture where the diversity, expertise, and collaboration of our team members drive shared growth and success
Read More >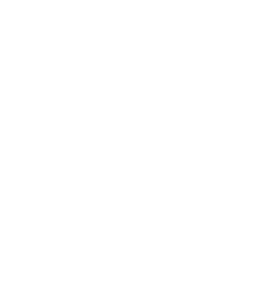
Customer-Centered Innovation
Developing innovative and resilient solutions to navigate the energy transition and help our customers keep the power on around the world
Read More >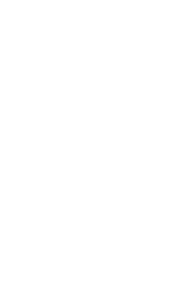
Operational Excellence
Embracing our principle of Responsible Stewardship to demonstrate our commitment to sustainability in all areas of our operations and solutions
Read More >